Isolator switches are used to ensure the safety of electrical systems during maintenance or malfunctions, but many people don’t fully understand the concept of disconnect switches.
So this article will clear up the confusion for you.
If interested, click here to know what is a timer switch?
What Is an Isolator Switch
An Isolator Switch is an electrical component used to ensure that electrical equipment is completely disconnected from the power source when it is being serviced. The isolator can be used to shut off the power supply to ensure the safety of maintenance personnel when they are performing electrical maintenance.
According to the different functions, isolator switches can be categorized into DC isolator switches and AC isolator switches. Before choosing to buy, you have to check your power supply type (AC or DC) in advance, because isolator switches for different types of power supply differ in handling arcs and disconnecting mechanisms.
For example: the voltage and current of AC power has a periodic variation that passes through zero each cycle. This periodic variation makes it easier to control arcing when breaking a circuit because the arc can be extinguished more easily as the voltage naturally passes through zero.
DC voltage and current are constant and do not pass through zero as AC does. This leads to the possibility of sustained arcing when disconnecting DC circuits without proper design. For this reason, DC disconnect switches require special designs to quickly and safely disconnect currents, such as contacts made of special materials or additional arc quenching chambers.
Of course there are also some other selection factors which I can mention below.
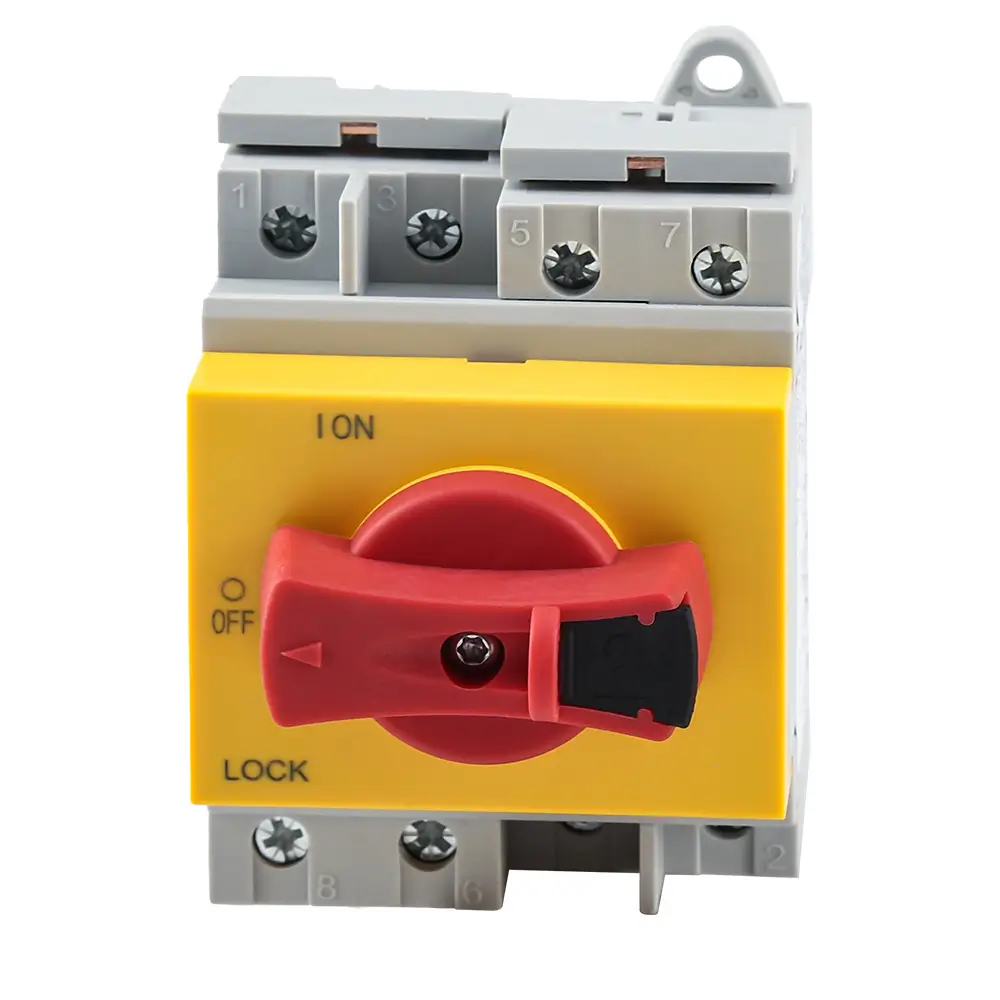
How the Disconnecting Switch Works
The isolator switch closes the circuit using an operable switch, which ensures there are no conductive contact points. This ensures safety during maintenance or inspection of equipment.
Let’s have a look at some specifics of how it works.
1. Mechanical operation
The disconnecting switch is usually driven by an operating handle or wheel by which the operator can control the moving parts inside the switch. These moving parts usually consist of rotating or sliding contact arms for physically breaking or connecting circuits.
2. Contact separation
When a disconnect switch is operated in the “on” state, the internal contacts are physically separated. These contacts are usually designed so that they remain visible after complete separation, ensuring that the operator can visually confirm that the circuit has been disconnected. The design of the contacts ensures that they are quickly and clearly separated when the switch is operated, thus avoiding arcing.
3. Safety locking
For added safety, the disconnectors can be locked in the “open” state. This is usually achieved by means of a safety locking device or a special locking mechanism that prevents the disconnecting switch from being inadvertently closed during maintenance. This is particularly important as it ensures that the system is absolutely safe while maintenance work is being carried out.
4. Disconnection without load
Disconnectors are designed to operate in a no-load condition. This means that they are not used to disconnect an operating electrical load, but are used after the electrical equipment has been shut down to ensure physical isolation when no current is flowing through the switch. The purpose of this design is to avoid dangerous arcing when separating the contacts.
5. Arc suppression
Although disconnect switches are not designed to handle load currents, under certain circumstances (e.g., improper operation or system anomalies), arcing may still occur during operation. Therefore, a high quality disconnect switch will be designed with an arc suppression or quick disconnect mechanism to minimize any safety risk.
In this way, the disconnect switch ensures that the power supply can be safely disconnected when the electrical system requires maintenance or overhaul, providing a safe working environment for maintenance personnel.
Scenarios in Which Isolators Are Used
Disconnect switches play an important safety role in many scenarios and are used in many scenarios, I have listed some out.
1. Industrial facilities: In industrial environments, disconnect switches are widely used to control and protect heavy machinery and electric motors. They make it safe to disconnect equipment during maintenance to avoid electrical accidents.
2. Substations and Distribution Systems: Disconnectors are used in substations and distribution systems to isolate high voltage circuits and ensure safety when performing line maintenance or equipment replacement.
3. Power plants: in power plants, disconnect switches are used to isolate generators and other critical equipment for safety inspections and maintenance.
4. Solar power systems: in solar power systems, disconnect switches are used to isolate the DC power supply during maintenance or inspection of photovoltaic panels and inverters, preventing safety risks caused by current backflow.
5. Buildings and residences: in commercial buildings and residences, disconnect switches are used for the safe maintenance of air-conditioning systems, heating systems and other large appliances.
6. Marine and heavy transportation: In ships and other heavy transportation vehicles, disconnect switches are used to control and protect electrical systems, ensuring that power can be cut off quickly and safely in the event of an emergency.
7. Chemical and refineries: In these high-risk environments, disconnect switches ensure that all equipment is safely isolated from the power supply when work is being carried out in high-voltage or hazardous areas.
The selection and use of disconnectors in these applications requires consideration of a number of factors such as voltage level, current capacity, environmental conditions and safety regulations to ensure safe and reliable operation. In this way, disconnect switches are recognized globally as a key piece of equipment for electrical safety and maintenance efficiency.
Isolator Vs Mcb
Isolator (Isolator) and Micro Break (Miniature Circuit Breaker, MCB) are two common electrical devices that have distinctly different roles and uses in circuits:
1. Function
- Isolator: It is mainly used to safely isolate electrical equipment and circuits in a state where there is no electrical load on the circuit to ensure the safety of personnel when maintaining or overhauling the equipment. The isolator does not have a breaking function, i.e. it cannot automatically break the circuit in case of current overload or short circuit.
- Micro break (MCB): is an automatically operated switch used to protect circuits from damage caused by overloads and short circuits. It is capable of automatically disconnecting the power supply when abnormal current is detected, thus preventing electrical fires or equipment damage.
2. Usage occasions
- Isolator: mostly used in high or medium voltage circuits, such as power distribution rooms, substations, etc. It is used to provide a clear visual disconnection point for equipment maintenance.
- Micro break (MCB): widely used in low voltage circuits in home, business and industry to protect wires and equipment from damage caused by excessive current.
3. Mode of operation
- Isolator: Usually manually operated and requires manual opening or closing.
- Micro breaks (MCB): are usually automatically operated, but can be manually controlled to break or restore a circuit.
In general, an isolator is more of a physical disconnect used to ensure safety, while a micro-break is an automatic circuit breaker used for circuit protection.
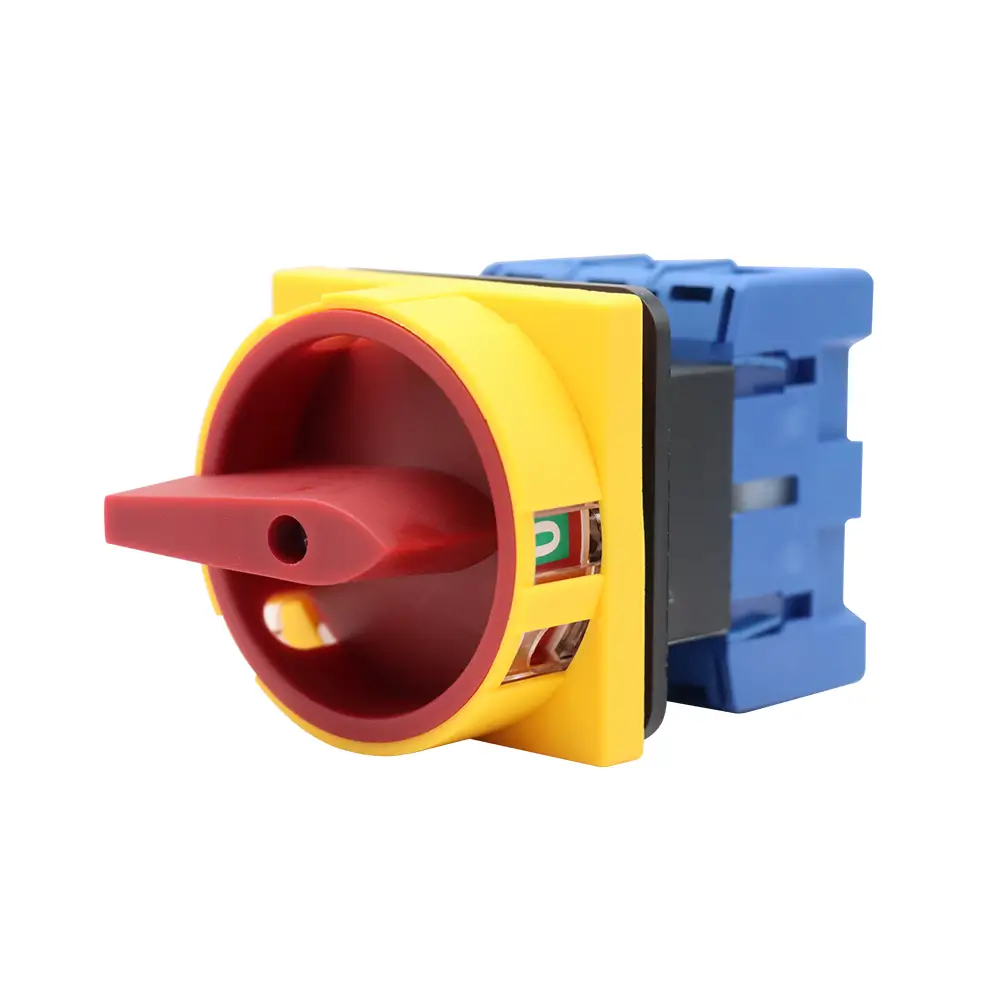
How to Connect the Disconnecting Switch
The steps for connecting a disconnect switch require strict adherence to safety codes, and the following is a detailed installation and wiring guide:
Tools and Materials Required
- Disconnect switch
- Screwdriver
- Wire strippers
- Voltage tester
- Suitable wires (choose the right gauge according to the circuit requirements)
- Connectors (if required)
Safety Precautions
- Disconnect the power supply: Before starting any work, make sure the power is turned off on the main switchboard or fuse box to avoid electrical hazards.
- Test for voltage: Use a voltage tester to verify that there is no voltage in the cables you will be working on.
- Follow local electrical codes: Follow the electrical codes and regulations in your area.
Wiring Procedure
1. Choose the right disconnect switch: Select a disconnect switch that meets the voltage and current specifications of the circuit you are working on.
2. Prepare wires: Use wire strippers to strip the insulation from the ends of the wires you will be connecting to the disconnect switch, usually exposing about 3/4 inch of bare wire.
3. Mounting the disconnect switch: Mount the disconnect switch on the wall, panel or distribution board as required. Make sure it is securely fastened and easy to operate.
4. Connect wires:
- Usually the disconnect switch will be clearly marked with terminals for incoming (power supply) and outgoing (load) wires.
- Connect the incoming wires (power cables) to the terminals labeled “L1” and “L2”, depending on whether the power supply is single-phase or three-phase.
- Connect the outgoing wires (to equipment, appliances or further circuits) to the corresponding terminals, usually labeled “T1” and “T2.
5. Ensure that the connections are secure: Make sure that all terminal screws are tightened so that the wires are securely fastened. Double check to make sure there are no loose connections.
6. Cover and label the switch: After all connections have been made, put the cover back on the disconnect switch. Label the switch to clearly mark what it controls or its location in the circuit.
7. TEST INSTALLATION: Turn power back on at the main switch. Operate the disconnect switch to make sure it works correctly, watching for unusual noises, odors, or signs of sparking.
8. Periodic Maintenance: Inspect the disconnect switch periodically to ensure that it remains in good working order, especially if it is located in a harsh environment or under heavy load.
By following these steps, you can connect the disconnecting switch safely and efficiently. Always prioritize safety and compliance with electrical standards and local codes. If you are unsure or uncomfortable performing electrical work, we recommend consulting or hiring a qualified electrician to perform the work.
Buying Tips
If you want wholesale isolator switches, there are two points I need to say.
The first point is to look for reliable manufacturers or suppliers who can provide high quality products. Consider the supplier’s production capacity, delivery time, quality control standards and after-sales service. After comparing the prices, product quality and services of different suppliers, choose the most cost-effective partner.
Consider us, which has received wide acclaim for both productivity as well as the quality of our products. In addition to selling Isolator Switch, we also sell EV chargers, Energy Storage, etc. Come and inquire!
The second point is that you have to make sure that your wholesale disconnect switches meet international and regional safety standards and certifications, such as CE, UL or ISO. Considering that different countries and regions may have different regulations and standards, it is necessary to know and comply with them.
Lastly, if you still have any questions, you can contact us and we will reply to you online 24 hours a day to ensure safety and efficiency!